Out of streets to factory shops: LED display boards
Our magazine wrote repeatedly about new applications in the area of LED technology, especially LED screens and signs. This time we decided to focus on their use in factories and other industrial areas where it is necessary to inform personnel about changing situation immediately. The magazine Sign Industry devoted an article by Louis M. Brill to this new and interesting topic. We understand only too well that this application has not yet reached Russia. But then it’s just a matter of time.
In today’s business climate, communication needs have to be instantaneous, interactive and proactive allowing employees to create timely decisions based on up-to-the-minute facts of the manufacturing process as it massages raw materials into a properly managed production cycle of finished goods.
Anybody who’s been in a typical factory during a production shift knows that most manufacturing processes are somewhat chaotic, very noisy and often hard for workers to communicate to each other directly on the shop floor. Other than pre-shift meetings, basic communications for workers was from plant signs that included charts, spreadsheets, diagrams and white boards that were posted on walls and bulletin boards. The major issues were basic concerns about safety, security and production goals. Up-to-date was more a situation of knowing how fast a sign can be changed and replaced.
LED display boards: Visual Factory system
The important part of this procedure is how workers keep in touch with the manufacturing process, which they do through a communication process known as the Visual Factory system. What that is about, in a nutshell, is the use of electronic signage as part of a human/machine interface that makes factories a productive and safe environment for its employees. More specifically, it’s a way of using signage to acquire a complete “snapshot” of a factory manufacturing situation that allows employees to learn within five minutes or less the pertinent details of who, where, when and how of what’s going on within that work area. Here sign messages are more than just safety platitudes, but a proactive medium that can set worker productivity goals, communicate safety messages, monitor production via inventory levels, and act as a real-time warning system in the extent of a manufacturing line slow down or plant accident.
In a nod to high-tech display processes, factories are discovering LED signage as an improvement in maintaining production and motivate workers on a daily basis. What the signs offer are an ease of visibility with very large, clear and multi-colored words that can be viewed from great distances within a factory work area from just about anywhere that there is a clear sight line to the sign.
Electronic signage is changing the relationship between plant workers and the manufacturing process by creating smarter workers. As these LED display boards output their content, they are providing a continuous report on factory conditions, the data coming from automatic sensors and sometimes even manual input. The LED signs and LED display boards are proactive as everybody on the factory floor can see them and if there is a quality problem, a slowdown or maintenance issue, the sign can also identify the nature and the location of the problem. Visual Factory (VF) signs are also interactive. The sign message (a quality or maintenance problem) triggers a worker (who responds to a situation), which triggers another message (problem solved!), which triggers another action (worker goes back to normal routine).
Smart LED display board
Electronic signs are also “smart” where a factory line sensor can monitor a production line process, summarize it and display the results. A case in point is where an sign or LED display board is tied into a controller on a production line and if a quality concern message shows up and is not acknowledged and responded to by a certain period of time, the board will actually shut down the production line.
Adaptive Micro Systems of Milwaukee, Wisconsin is a manufacturer of LED displays and marquees primarily used for commercial, industrial, public transportation and automotive manufacturing businesses. One aspect of their electronic sign display strategy is the Visual Factory (VF) communicating system, which was explained by key account sales manager, Gary Wells. Wells noted it is a dedicated signage process that presents production, planning, manufacturing and warehousing summary information that allows workers and management to maintain manufacturing operations at peak efficiency. Already, he says hundreds and hundreds of these systems have been implemented in manufacturing plants around the United States.
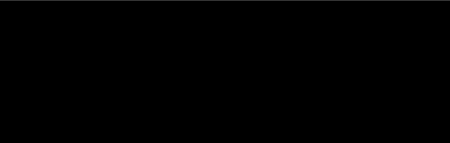
LED display board
Photo credit: Adaptive Micro Systems
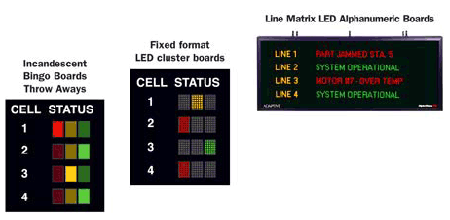
LED display board migration
Photo credit: Adaptive Micro Systems
The actual nuts and bolts of the Adaptive Visual Factory system as explained by Gary includes a series of LED display boards and marquees (four or more line display boards) that are systematically distributed throughout each factory area in plain site for anyone to read them as they need to. The LED display boards are keyed in turn to various factory machines and sensors or spreadsheets that convey current factory manufacturing data about production quotas, inventory levels of parts, scrap levels, job starts and deadlines. On the sales side, it could indicate what new sales orders may be coming up with priority ones marked in certain colors, etc. Information outputs include any factory information that can be presented as alphanumeric data to factory employees. The information is all real-time and as the factory processes change, so does its data displays to keep up with these changes.
![]() |
![]() |
LED display boards Photo credit: Adaptive Micro Systems |
The number of LED display boards and marquees used in any particular factory depends on the size of the factory work area, the amount of floor acreage to be “hooked” into a LED display system and the amount of data required to be transmitted to factory operating staff. Thus as one factory might require 5 displays and one or two marquees, another, larger factory may require 15 displays and five marquees to accomplish a similar task of communicating to their workers.
Adaptive reader board LED signs and marquees are usually installed by distributors who literally handle the nuts and bolts of designing and placing client-specific electronic LED signage within their plants. One company who is a major integrator of the Visual Factory concept is Electro-Matic Products out of Detroit, Michigan. The company is an electronics and electrical distributor of control systems for manufacturing processes for automotive, commercial and manufacturing industries. Using mostly LED display boards, as explained by Sande Weiler, a visual and wireless product manager, the company designs electronic signage systems that help manage various manufacturing processes.
“We work with the major automotive manufacturers to create electronic signage applications to display pertinent information about their production counts, their ability to monitor machine faults and to provide safety and inspirational messages to their workers on a continual basis. One of our clients, Daimler-Chrysler sees its use of VF as a “mission critical” process where it is less a sideline display and more a part of how they run their manufacturing plants.”
Another distributor of Adaptive products is Lakeland Engineering Equipment Company (Minneapolis, MN) also a distributor for integrating control systems into manufacturing facilities. Dean Horejsi (pronounced Horsh), VP of Lakeland’s Advanced Technology Group says, “In the old days of manufacturing (5-10 years ago), factory signs were not as proactive and interactive as they are now, but current manufacturing processes are almost demanding that level of control today. As plants are becoming more automated and getting fewer people to do more tasks, the employees who are there, definitely need more specific information during their workday as they do their jobs.”
Getting product information and production data in real time has become a competitive difference, Dean cites some customer applications where Visual Factory sign systems have improved a company’s productivity. John Deere, a manufacturer of farm equipment, shows off their manufacturing cycle to their workers to indicate (to the moment) when deliveries of new parts are needed at the production line. At 3M, the VF system is employed in maintenance to show off a visual alarm system indicating line problems and locations of these problems.
The future of LED display board Visual Factory systems
As for the future of Visual Factory systems, Dean believes that the process is only in its beginning stages, “as factory managers begin to understand more of how to use LED display boards in this setting more of it will be used to better define the manufacturing output and the work environment”. Electro-Matic’s Sande Wieler agrees, “in terms of the limits of what electronic signage can do, this is the tip of the iceberg. I think there’s room for huge improvements in how LED display boards will be employed. Most of these changes will come from the software that manages the sign’s content, greatly increasing the human/machine interface and its ability to manage the manufacturing process.”
Already the use of Visual Factory signage systems is making a difference in most manufacturers capabilities says Adaptive’s Gary Wells. “Our customers reaction to inheriting these LED display board systems is always positive. In every case, a new customer will see anywhere from a 10-30% productivity improvement which allows them to reduce scrap accumulations, to reduce work-in-progress throughput times and to manage their inventories better. Properly used, a VF system provides a global overview of that factory’s manufacturing process so everybody knows the functionality of the factory as it is happening.”
It’s a long way from posting charts on bulletin boards, but with a good Visual Factory system in place workers know in a few seconds what used to take days to find out, and the best news, the signs don’t take lunch breaks or require overtime for a 24/7 shift. And that’s a sign that every one likes.